Project: Schools Wind Tunnel
20th
December 2010
The intention of this project was to see if I could develop
a desktop-size wind tunnel that might be usable in schools or colleges.
By background I'm an aerospace engineer and I thought that this
might be somewhere I could add some value. I did manage to get a
working wind tunnel although I didn't manage to get some of the
experiments I'd hoped for working. I made the tunnel with
laser-cut plywood from Ponoko and the models for the test section were all 3D printed at Shapeways.
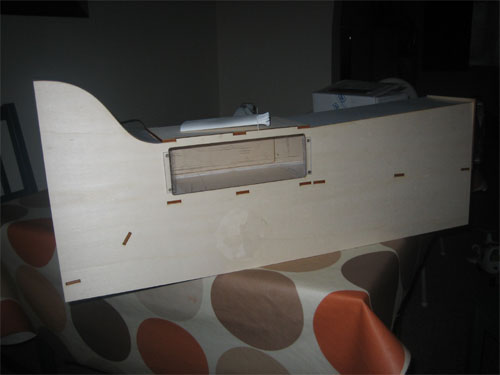
Wind tunnels
are not new, they've been around since the dawn of flight. They
are designed to allow testing of a model, be it a whole aircraft (or
building, bridge, antenna, ...) or a part of one, like a wing section
in a uniform, controllable air flow. This can be important
because it can allow direct & repeatable measurement of forces,
moments, pressures or flow patterns around the model.
Small-scale,
low-speed wind tunnels aren't always that useful unless you're only
interested in small-scale models. Extrapolation to full-size
doesn't always work since some flow effects don't always scale very
well. However, I wanted to make something for demonstrations
only, so accuracy wouldn't that important.
[Before
I go into the design and construction of the tunnel - a
note: you'll see that some of the pictures have been fiddled with,
this isn't anything sinister, it's just to remove from the tunnel a logo from the place
I work. I built this tunnel for a work open day but I'm not sure
that they'd want to be on my website so I've removed it on all the
photos where it's visible]
Wind tunnels can be set up as a closed-loop or open; this tunnel is of the open type since this is a lot simpler.
The
arrangement is simple; there is a large area intake followed by a
relatively sharp contraction down to the test section (where models
will be placed) followed in turn by a shallow expansion of the tunnel
duct up to the fan (called the diffuser).
The fan is always at
the back to draw air past the model, it never blows onto it since the
air coming from a fan is always stirred up from the rotation of the
fan; this would ruin any measurements that you tried to take from the
model.
It.he tunnel was designed to be laser cut from two 4mm thick "P3"-size plywood sheets by Ponoko. I designed the tunnel in Solid Edge,
a parametric 2D CAD system available for free from Siemens PLM (there's
a paid for 2D version with access to an API that allows automation and
a paid 3D version that I haven't used but which is supposed to be quite
nice).
The parametrics are really nice to have for something like this
since I was able to set up the general layout of the tunnel and then
play around with the dimensions until I got the largest design that
would fit on the available sheet size, with the parametrics retaining
all the shapes and connections automatically.
Because Ponoko needs the designs to be submitted as EPS files I needed to convert them, to do this I used Inkscape.
I was able to copy and paste the designs across from Solid Edge
but the scale didn't work perfectly. To fix this I made some
marks in Solid Edge exactly at the corners of the P3 sheet size and I
was then able to align these with the corresponding corners of the
Inkscape template files provided by Ponoko (these files, along with the
others needed, are available at the end of the article below if you
want to use them).
The tunnel ended up about 700mm (a bit less
than 30") long and 300mm (approx. 12") high with a test section about
100mm high and 120mm wide. The test section is quite long, onger
than really needed to allow a wider angle of view into the centre of
the test section from the sides, front and back. This was
intended to allow more people to see in than might be possible were it
to be smaller.
To keep the construction simple all the area changes take place in one plane, the only change being in height. This will definitely
reduce the quality of the flow, but it simplifies the construction and
design by an order of magnitude; I decided that this was a good trade
given the end use I had in mind for the tunnel.
I
designed the contraction and intake to allow a flow conditioning pack
to be installed - this is a combination of fine screens and honeycomb
to smooth out and straighten the flow - but in reality this isn't
needed and I would have been better off putting in a proper bell-mouth
intake...
I had a
difficult choice to make for the fan I would use, I looked into lots of
different options. The main considerations were cost, simplicity,
safety and availability. Fans that are very powerful are
dangerous, they can cut to the bone (or worse) and they also require
significant power supplies that bring dangers of their own and also
extra cost.
In the end I decided to use a 120mm computer
case fan. The main reasons for this are: they're easy to get,
they're cheap, they don't require ridiculous power supplies and they
run from 12V. I also had one hanging around already, which was
another reason for me to use one. PC case fans are also (with suitable
guarding) relatively safe, or at least my one was - I've
unintentionally stopped it with a finger a few times with nothing more
than bad words and a red mark as a result.
I bought a
simple "wall wart" AC adaptor that I could adapt to fit the fan which
wanted 12V DC; this also meant I wouldn't have to mess with anything at
mains voltage (I'm not an electrician and, unless you are, I'd
recommend not taking on mains wiring). 12V should be relatively safe
but please don't adapt the wiring of anything you've bought unless you
know what you're doing since you may still find a way to hurt yourself.
Construction
The
laser cutting went quite well, the only problems were with the logo cut
into the side, which no-one else would need anyway. The parts were well
cut and packed.
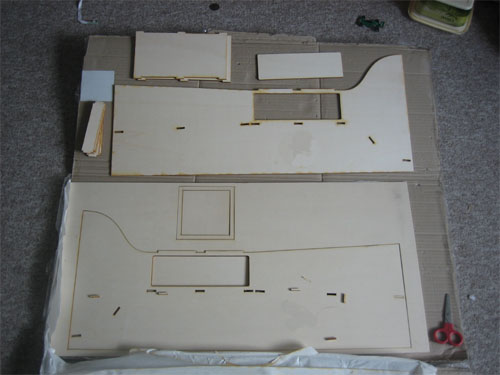
The
fit between the laser cut parts was really precise, all the parts were
able to dry fit together with
no filing or adaptations needed. The sheet also seemed to be very
close to the 4mm nominal, I'd included little bumps on the slots to
take out tolerances of the tabs and these gave a good friction fit.
I've not had contact with laser cutting before and I confess I
was really surprised by how accurate and easy it all was.
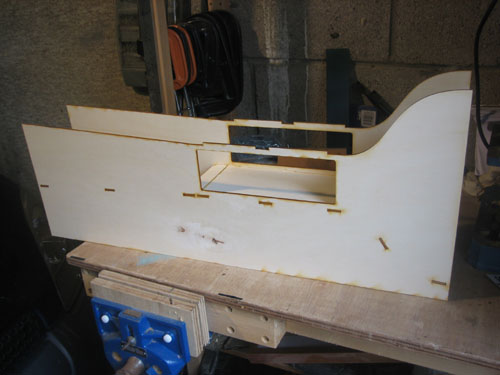
The
design as it stands does not include any laser cut plastic for the
windows in the test section; I ended up
making these from polystyrene sheet I had left over from another
project.
Ponoko carry acrylic sheets and it would be easy to design
windows to fit. The ones I made were cut with a jigsaw and finished by
hand with a file using the ply panels cut from the window holes as
templates. I made some rectangular pieces that I glued over the
edges of the panels, leaving an overlap that I could use to drill and
then put a screw through into the wood behind.
The
tunnel uses cardboard to make the top and bottom sides of the duct,
simply glued into place. To seal some gaps between the cardboard
and the plywood I used some decorators caulk sealant.
I
discovered quite quickly that I hadn't really put enough thought into
the fan mounting. In the end I used the piece I'd had laser cut
andwiched together with a part cut from the plywood sheet that was not
laser cut. If I had time to iterate the design I'd improve this
part. The motor bolts into place with a metal fan grille over the
top to protect fingers from the blades.
In the end I also added
some lights to the test section - I used some flat LED patches that I'd
bought at Ikea ages ago for our kitchen (they turned out to be rubbish
for the kitchen but perfect for the tunnel). Lighting makes it
much easier to see what's going on in a demonstration and I'd recommend
it.
Models - the best laid plans...
I'd intended to be able to measure pressure changes around a wing section and demonstrate them using an array of u-tube manometers.
The idea would be to measure pressure all around a wing section
and then display it to show the low pressure on the top and the higher
pressure on the bottom of a wing and then show how this changes when
the wing stalls (when flow can no longer follow the top surface of the
wing - for more explanations on this and more please see this excellent site).
I was a little unsure that this was a good idea since the 'low
pressure on the top sucks the aircraft into the air' model for lift
generation isn't my favourite but I thought it would make a good demo
if nothing else.
So: I needed a wing section, here I turned to Shapeways.
I designed a wing section with integral pressure tap tubes and
had it 3D printed. This is a brilliant use for 3D printing, it's
absolutely what it's best at. The first time I met 3D printing
was at the low-speed wind tunnel at work where they hard started to use
it to make parts for wind tunnel models. If you want to measure
pressure around a model you need a tube that will allow you to access
the surface at that point, this is known as a pressure tapping. A
hole in the surface of the model will be connected, via a tube, to a
pressure guage. The really nice thing about 3D printing is that
you can build all of
these tubes and holes in the model in one piece and save a huge amount
of work.
My wing turned out really well except in one way - it didn't work.
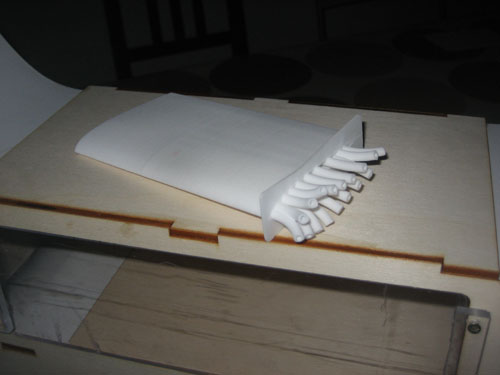
It didn't work for a few reasons:
Why it didn't work #1 - wrong choice of material The
material I chose, without really thinking, was the Shapeways "white,
strong and flexible" Nylon plastic. This is normally excellent
and quite cheap. However it's also laser sintered from powder and
some of the powder that wasn't melted together wouldn't fully come out
of all of the fine tubes; blocked like this the pressure tappings would
never work. The other problem is that this material is slightly
porous and the leaks this would allow would be a disaster for the
pressure measurements. If you want to do something like this use
some of the liquid-based non-porous materials (I think "transparent
detail" might be suitablem, check the material details of your 3D
printer for a final check).
Why it didn't work #2 - wrong speed & rubbish manometers When
I finally realised that my beautiful pressure tapped wing wouldn't work
I hacked something (literally) out of softwood to test if I could have
got a measureable pressure change. Turns out that I wouldn't have
anyway. The speeds I was getting in the tunnel were not large and
so the pressure changes that I could get were correspondingly small.
The manometers I built to test simply wouldn't measure pressure
changes that small. It might be possible to measure these
pressures but not with homemade equipment (at least not homemade by me
anyway).
Why it didn't work #3 - where I become even more embarassed... To
provide the final nail in the pressure-measurement coffin I built the
wing as a mirror image of what I really wanted. That's all I have
to say about that.
Models - what I did in the end
What
I actually did was to adapt the very first 3D print I'd ever had made -
a model of a wacky aircraft I came up with as a demonstration of how
you can learn from even the silliest-looking concept. I'd put
this in the tunnel with a stand made from polystyrene and show some of
the flow patterns around the aircraft using a wool tuft.
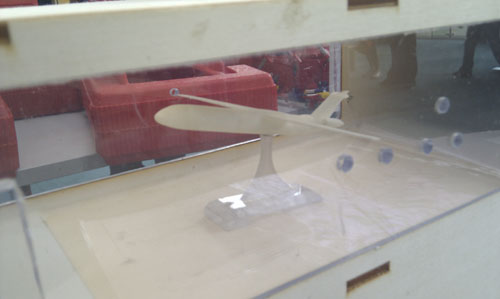
The above photo doesn't really give you the sense of the silliness of this model so I'll show a three-view below:
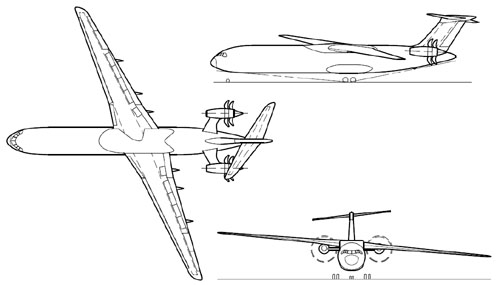
It
really is very silly and no-one would ever want to build such a thing,
but it has some subtle good points to go with its
glaringly obvious bad points; how long it takes for people to work
out what these are is always an interesting measure of how they
approach a problem...
To my suprise this worked a treat!
The model sits at incidence in the tunnel and it's possible to
prove that it's producing lift by checking behind the wing tips - the
wool tuft happily spins around showing the tip vortices. It's also possible to show the slight upwash in front of the wing and the downwash behind the wing.
The
lights in the tunnel make the model and the motion of the wool tuft
(just a stick with a bit of cotton and a tuft of wool on the end)
really clear.
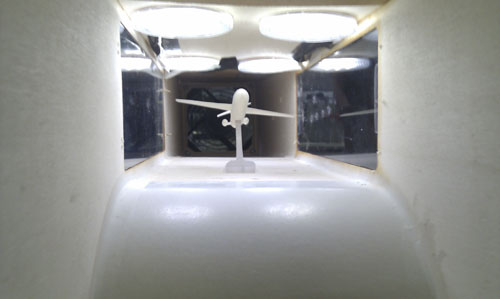 (I'm
quite pleased with this picture into the test section - it's quite hard
to see the scale and could easily be a lot bigger than it is :)
Files
So you think you want a wind tunnel? All the files that you might want to make this one are here.
Because
I've finished with the project and I hope you might be able to get more
use out of it I'm releasing all of the files linked to below under a Creative Commons Attribution-ShareAlike license.
For full terms please follow the link above, but in summary: you
are free to share and remix the work I've done as long as you credit me
and license the work you do under the same terms.
Wind tunnel - Zipped PostScript (*.eps) files for Ponoko and source Inkscape SVGs are here
Wing model (that didn't work so well for me, your mileage may vary) zipped *.stl file is here
For the power supply something like this would probably work
For the fan, you might try something like this
but go for more power if you can (within the computer fan realm Delta
fans are probably the most powerful I've seen) - remember to get a fan
guard!
I'm
not releasing the design or 3D printing file for the aircraft because the model
required some adaptation before I could use it (clipping the wings back
to a smaller span, for example) and its wacky configuration wouldn't
help most people to explain the principles involved. If there's a
big demand I might be able to set something else up, feel free to tweet
something to @fastness or send me a mail.
|
|
|
|
fastness
- Iain Banks Graphics
All of the content from my Iain M Banks website, now
shifted to be a section in this one
fastness
- Links & Resources:
Processing:
An open source programming tool aimed at artists,
engineers and designers. Simple, light and Java-based with a
wealth of libraries and a strong user community
Shapeways:
3D
printing for the masses - plastics and metal to your design or team up
with a desigenr to personalise a design with a 'co-creator'.
Visit my Shapeways
shop for some things I've designed.
Meshlab:
MeshLab is an open source, portable, and extensible
system for the processing and editing of unstructured 3D triangular
meshes
Blender:
Blender
is the free open source 3D content creation suite, available for all
major operating systems under the GNU General Public License
Gimp:
GIMP is the GNU Image Manipulation Program. It is a
freely distributed piece of software for such tasks as photo
retouching, image composition and image authoring. It works on many
operating systems, in many languages
Inkscape:
An Open Source vector graphics editor, with
capabilities similar to Illustrator, CorelDraw, or Xara X, using the
W3C standard Scalable Vector Graphics (SVG) file format
Ponoko:
Retail laser cutting outlet with centres in New
Zealand, USA, Germany, Italy and the UK (if not more by now)
Eclipse:
Java development environment
|